Tired of cumbersome poultry skinning systems that have to be dismantled every night to maintain hygiene? Meet the new Prime CSKB-1 Skinner, an ultra-hygenic, simplified solution that combines economy of design with innovations to remove those bacteria traps that have required frequent cleaning in all skinners until now.
Most, if not all skinners, are based around modular belts, which have to be dismantled and sanitized at the close of each day to ensure bacterial build-up does not take place. In contrast, the Prime CSKB-1 Skinner eliminates this problem by replacing the modular design with a seamless, sanitary belt, which can be cleaned by a simple hose down.
At the same time, Prime Equipment engineers have eliminated many components from the previous skinner design, meaning that many less pieces that could potentially fail or require replacement. With its improved simplicity, Prime estimates a 50% reduction in total MMR cost compared with the previous model (a design which is replicated throughout the industry).
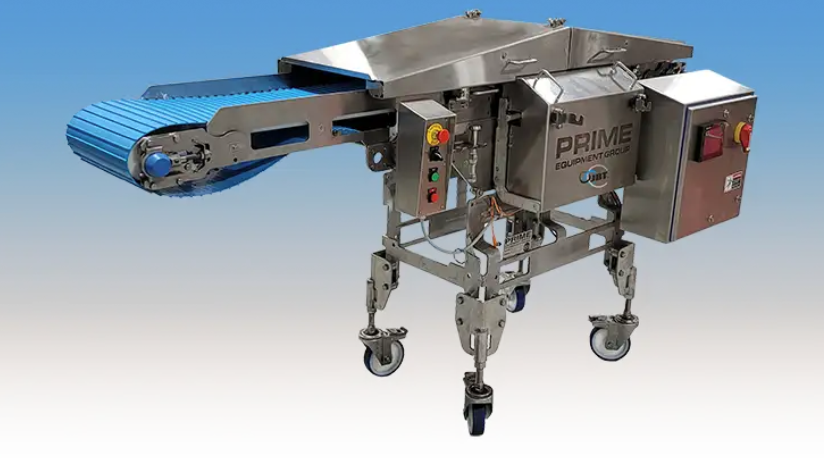
10-minute turnaround
Distilling the advantages, Prime Equipment’s Nick Gasbarro describes the sanitary belt as a step forward for the poultry processing industry. “The simplicity of the machine, which includes getting rid of the paddle wheel and the upper assembly, makes it an easier machine to manage, and this has reduced the Total Cost of Ownership of the Skinner as a whole,” he says.
“To take apart and reassemble the previous version of the Skinner for cleaning was probably a 35-40 minute process for one person and in a lot of plants you have 10-15 skinners; we have now reduced that to 10 minutes.”
When Prime introduced the skinner category, it succeeded in taking people off the processing line. With the new Prime CSKB-1 Skinner, Gasbarro says Prime is reducing the sanitation and maintenance time, which frees up employees to focus on other tasks.
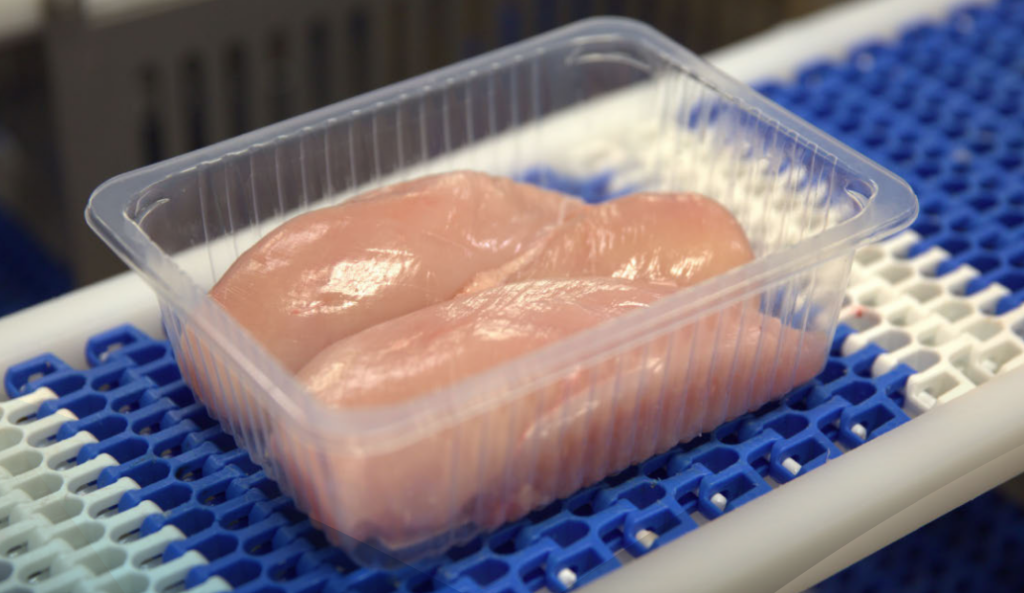
Revolutionizing skinning
Prime Equipment was started by Nick Gasbarro’s grandfather, Geno, father, Mike, and uncle, Joe, in the early 1990s. Whereas previously skinning chicken and turkey meats had been a labor-intensive task with a poor record on yield, Prime invented a solution that used a “paddle-wheel” shaped roller that automatically removed the skin in a far more effective way without losing valuable meat along the way.
“It was very revolutionary for the chicken industry and really created its own product category,” recalls Gasbarro. “It’s something we are very proud, particularly because it saved a lot of injuries to workers that had previously been common, such as carpal tunnel injuries.”
At this time, the Prime Skinner could be equally applicable to turkey as chicken, white meat and dark, but its initial modular design made it tricky to clean.
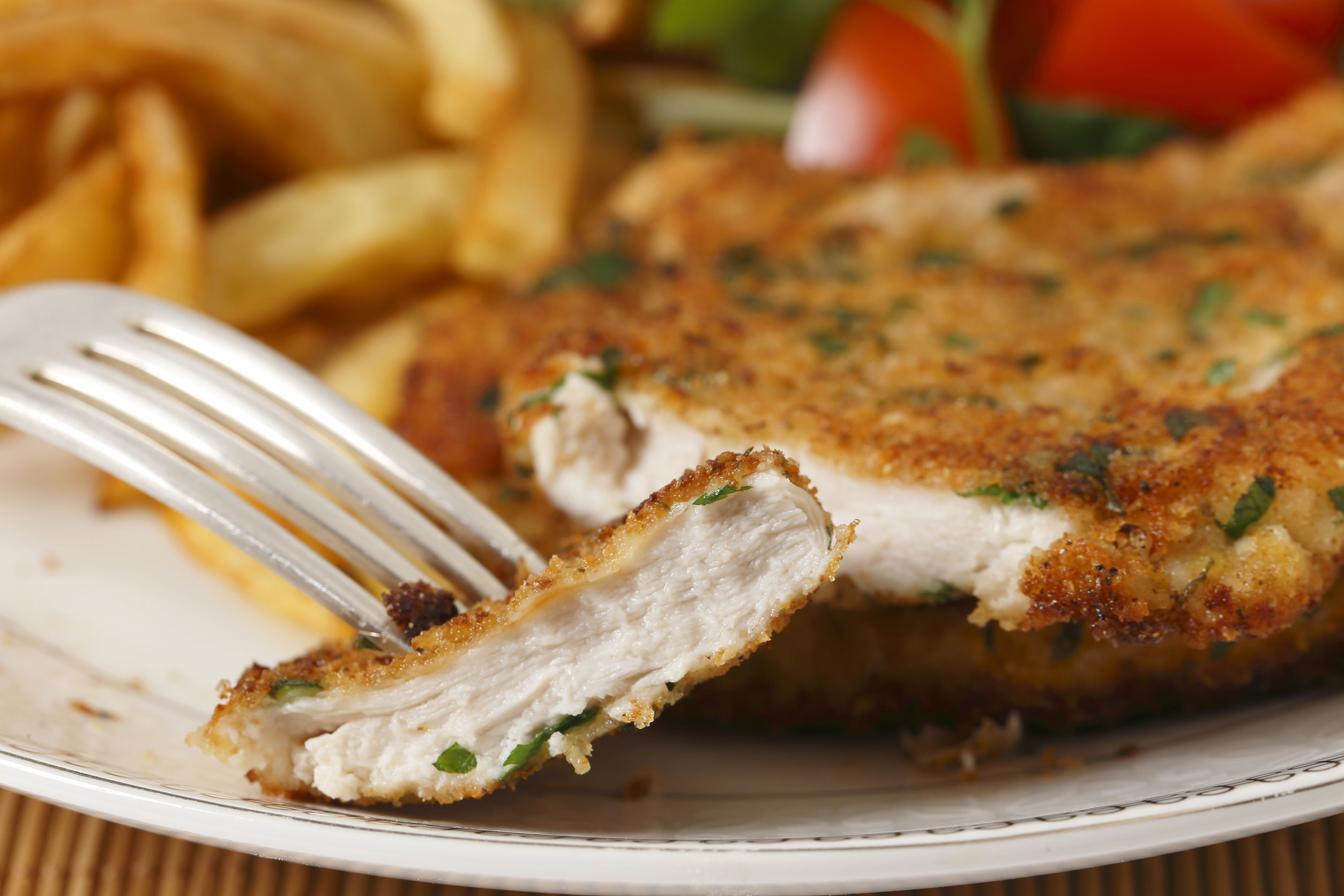
A new level of hygiene
With time, the design of Prime’s original skinner was replicated across the industry, but the cleaning challenge remained, regardless of manufacturer.
In response, Gasbarro’s grandfather – now in his 90s – has delivered a winning solution once again in the form of a seamless belt featuring flights to replace the wear-and-tear heavy paddle wheel, while at the same time performing the same function. Forming a key component of the new Prime CSKB-1 Skinner, the new belt brings new levels of hygiene to poultry skinning, with cleaning also be carried out by a simple hose down rather than dismantling the entire system.
“The old belts on our skinners and those being used across the industry are modular, so they can be bacteria traps and as a result have to be removed and sanitized at the end of each day,” explains Gasbarro. “With the new CSKB-1 Skinner, the seamless belt eliminates this problem and can be cleaned quickly and simply. Through this action we were also able to eliminate the upper assembly conveyance, which moved the product through the pinch-point, so that means one less moving part that has to be maintained.”
The new Skinner also features a switch from a traditional gear-and-motor drive system to a drum-drive: a single, self-contained motor with a much simpler drive system that lasts longer and uses less energy than the traditional gear motor drive. “We took a concept that was simple and we’ve made it even simpler,” Gasbarro adds.