Als der führende norwegische Geflügelproduzent Norsk Kylling seine neue Produktionsstätte plante, war das Ziel klar: Es sollte ein herausragendes Gebäude für die nachhaltige Lebensmittelproduktion und die norwegische Landwirtschaft entstehen. Aber sie wollten auch, dass alle an dem Projekt beteiligten Zulieferer sich für die Weiterentwicklung der Branche engagieren und einsetzen.
JBT verfügte über die Lebensmittelverarbeitungsmaschinen, die Erfahrung und die Innovation, die den Anforderungen entsprachen, und stellte ein engagiertes Team von Experten zusammen, das eng mit Norsk Kylling zusammenarbeitete. Als innovativen Teil des Projekts hat JBT den Ofen so umgestaltet Stein® TwinDrum Spiral-Ofen so um, dass sie elektrische Wärme aus erneuerbaren Quellen nutzen kann.
"Wir wollten eine der modernsten und effizientesten Fabriken der Welt in Bezug auf Qualität und Logistik schaffen", sagt Håvard Staverlökk, Projektleiter bei Norsk Kylling.
Für Norsk Kylling steht das Wohl der Tiere im Mittelpunkt. Gleichzeitig muss sichergestellt werden, dass die Produktion diesteigende Nachfrage nach Geflügelprodukten befriedigen kann, ohne dass dies zu Lasten von Klima und Umwelt geht. Sie arbeiten mit dem Kreislaufgedanken in der gesamten Wertschöpfungskette, angefangen bei der Frage, welches Futter das Huhn frisst, bis hin zur Verwendung der Nebenprodukte aus dem Schlachthof und der Nutzung der biologischen Vielfalt. Im Jahr 2016 begannen sie mit einer umfassenden Strategiearbeit für ihre zukünftige Entwicklung, die in einem ersten Schritt dazu führte, dass sie auf eine andere Hühnerrasse umstellten.
"Wir haben Ross, unsere bisherige Hühnerrasse, durch Hubbard ersetzt", sagt Håvard Staverlökk. "Das Hubbard-Huhn wächst langsamer und hat einen besseren Appetit und eine bessere Gesundheit, was zu einer besseren Tierhaltung beiträgt. Außerdem hat es einen besseren Geschmack. Die Umstellung war ein wesentlicher Bestandteil unserer Nachhaltigkeitsarbeit."
Zu Beginn der Strategiearbeit wurde auch klar, dass die Produktionsanlage mehrere Herausforderungen mit sich brachte. Es war unmöglich, die bestehende Fabrik so auszubauen, dass sie den künftig geforderten Nachhaltigkeitsstandard erfüllte, was zu der Entscheidung führte, eine völlig neue Fabrik zu bauen und Partner zu finden und auszuwählen, die Maschinen liefern konnten, die den neuen Standard erfüllten.
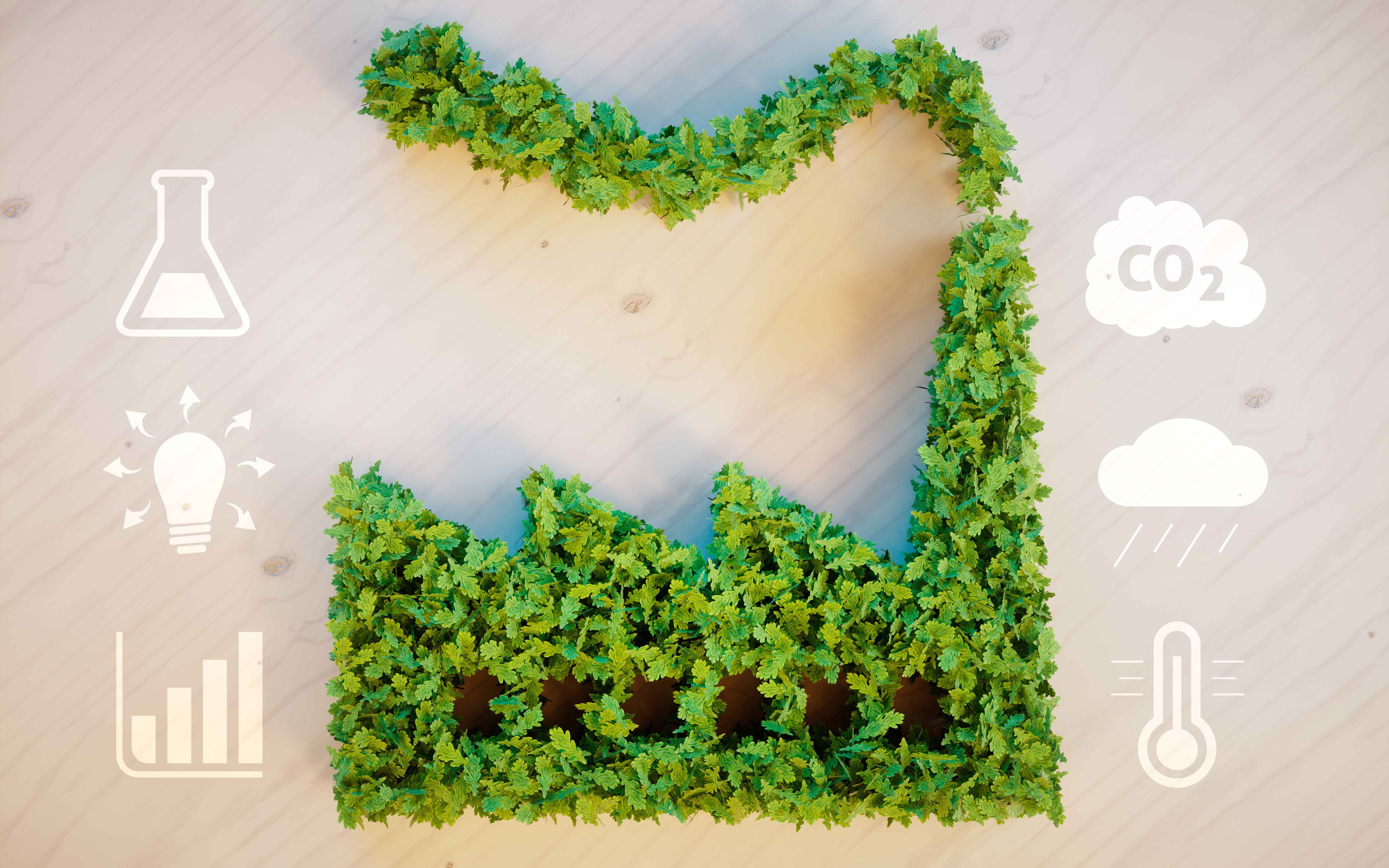
Intelligente Energielösungen im Mittelpunkt
Der Ehrgeiz bei der neuen Produktionsstätte war groß, was die Nachhaltigkeit betrifft. Sie sollte ein Modell für andere Hersteller auf der ganzen Welt sein, wenn es darum geht, sich an die Energiesysteme der Zukunft mit zunehmend ungeregelter Energie wie Solar- und Windenergie anzupassen.
"Wir haben unter anderem in die Elektrifizierung investiert und uns auf die Energieflexibilität konzentriert, vor allem durch Energiespeicherung", sagt Håvard Staverlökk. "Das Werk ist emissionsfrei gebaut und nutzt ausschließlich erneuerbare Energien, und wir haben die Treibhausgasemissionen im Vergleich zu unserer alten Fabrik um 100 Prozent reduziert."
Die Fabrik verfügt über mehrere intelligente Systeme zur Speicherung, Steuerung und Beschaffung erneuerbarer Energie. Es nutzt thermische Energiespeicher für Wärme, aber ein Projekt zur Entwicklung der Technologie, um auch Kälte speichern zu können, ist im Gange. Das Werk bezieht Fernwärme von der Elkem-Hütte auf der anderen Seite des Orkdalsfjords, deren Abwärme den gesamten Wärmebedarf des Werks deckt. Dank der Pipeline können auch andere Fabriken und Büros in der Umgebung ihren Bedarf an Strom und fossiler Energie zum Heizen reduzieren.
"Die Anlage ist emissionsfrei gebaut und nutzt ausschließlich erneuerbare Energien, und wir haben die Treibhausgasemissionen im Vergleich zu unserer alten Fabrik um 100 Prozent reduziert", sagt Håvard Staverlökk, Projektleiter bei Norsk Kylling.
"Die Pipeline ist das Ergebnis einer Zusammenarbeit zwischen der lokalen Industrie, Energieunternehmen und der Gemeinde", sagt Håvard Staverlökk. "Diese Art der Zusammenarbeit ist von zentraler Bedeutung für unser Bestreben, eine treibende Kraft im Bereich des Klimaschutzes zu sein. Wir haben unsere umweltfreundlichen Energielösungen so konzipiert, dass sie Energie mit anderen Fabriken und Büros teilen können, um die Klimabilanz weiter zu verbessern. Unser Ziel ist es, dass das gesamte Gebiet weniger CO2-Emissionen aufweist als vor unserer Ansiedlung."
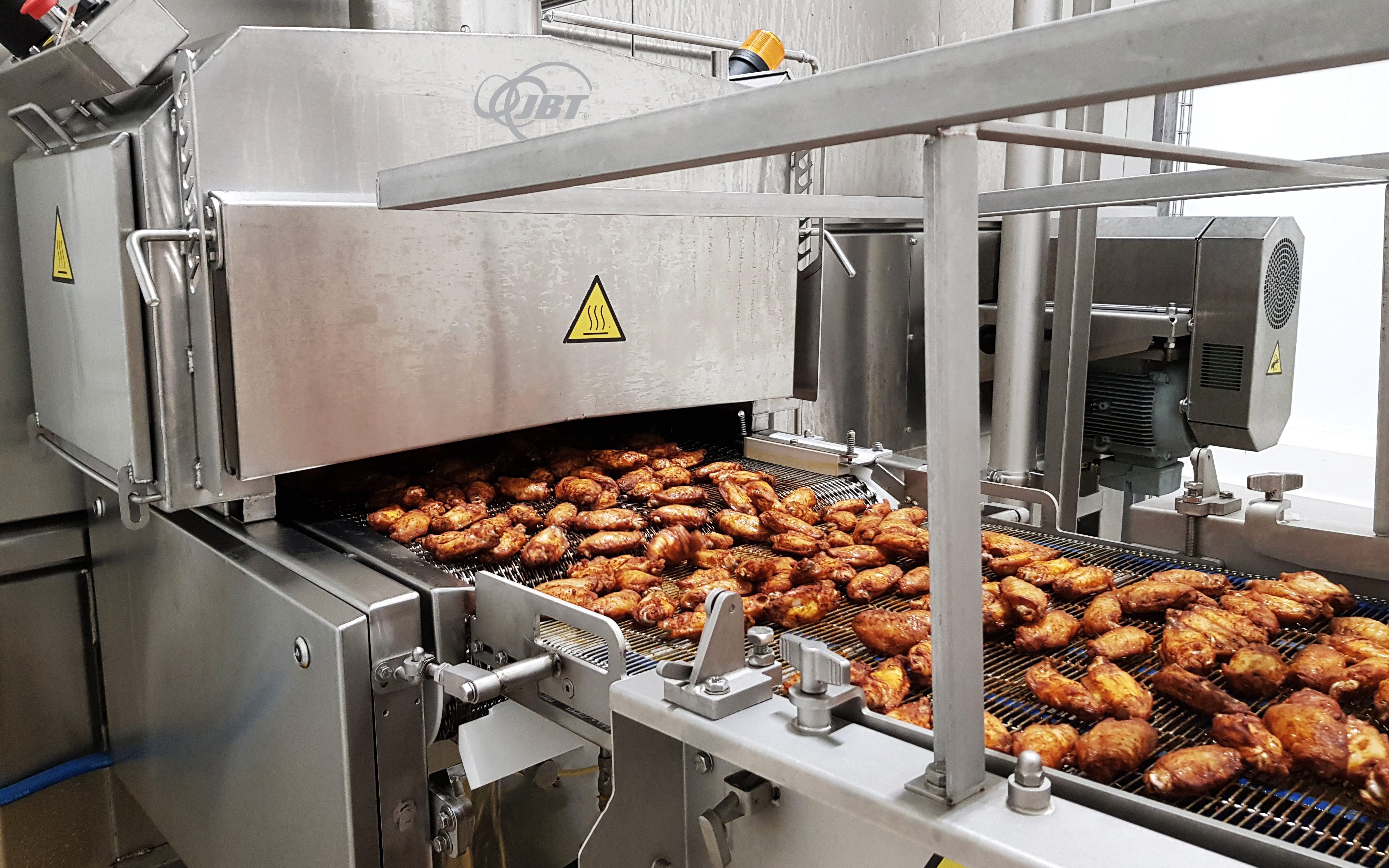
Nachhaltige Produktion mit einer einzigartigen elektrischen Linie
Norsk Kylling hat eine Produktion, die alles im Geflügelsegment umfasst, von der Produktion frischer Stücke bis hin zu gekochten Produkten. Auf der Weiterverarbeitungsseite der neuen Anlage hat JBT zwei integrierte, elektrisch beschickte Produktionslinien mit einer Stein M-Fritteuse, zwei Stein TwinDrum Spiralöfen und zwei Frigoscandia GYRoCOMPACT® Spiralfroster. Die kreative Herausforderung bestand jedoch darin, den Stein TwinDrum Spiralofen so zu modifizieren, dass er mit elektrischer Hitze betrieben werden kann, sagt Erland Leide, R&D Manager bei JBT.
"In Produktionsanlagen werden heute häufig Öfen mit thermofluidischer Wärmeübertragung eingesetzt, d. h. das Öl
wird mit Strom oder Gas erhitzt und dann in Kreisläufen herumgepumpt. Norsk Kylling wollte einen Ofen, der direkt mit Strom betrieben wird. Die elektrische Beheizung hat den Vorteil, dass der Wirkungsgrad höher ist und die Temperaturregelung schneller erfolgt, so dass der Ofen weniger Energie verbraucht. Sie können auf völlig fossilfreien und erneuerbaren Strom zurückgreifen, was es zu einer nachhaltigen Lösung macht."
Schon als JBT den Stein TwinDrum Spiralofen entwickelte, dachte man über die Nutzung von Strom als Alternative nach. Man kam jedoch zu dem Schluss, dass der Einsatz von elektrischem Strom in heißen und feuchten Bereichen eine große technische Herausforderung darstellt. Daher wurde er zunächst nur für die Beheizung durch Thermofluid ausgelegt. Auf der Grundlage des umfangreichen Lastenhefts von Norsk Kylling änderte JBT die Grundkonstruktion und baute den Ofen zum größten Elektroofen in Europa aus.
"Der Vorteil der elektrischen Beheizung ist, dass der Wirkungsgrad höher und die Temperaturregelung schneller ist, was bedeutet, dass der Ofen weniger Energie verbraucht", sagt Erland Leide, R&D Manager bei JBT.
"Eine Herausforderung bei der Verwendung von Strom zum Heizen ist der Strombedarf. Es muss viel Hochstrom in den Ofen geleitet werden", sagt Erland Leide. "So waren zum Beispiel acht dicke Kabel erforderlich, um die Heizelemente zu erreichen und zu versorgen. Bei anderen elektrisch beheizten Öfen werden die Kabel von der Decke bis zur Haube verlegt, wo sich die Heizelemente befinden, so dass sie sich beim Anheben des Ofens bewegen, was wir vermeiden wollten. Wir haben eine Lösung entwickelt, bei der die Kabel stattdessen im Inneren des Ofens verlegt werden. Auf diese Weise konnten wir sie statisch halten und den Verschleiß reduzieren, um die Lebensdauer zu erhöhen und die Wartung zu minimieren."
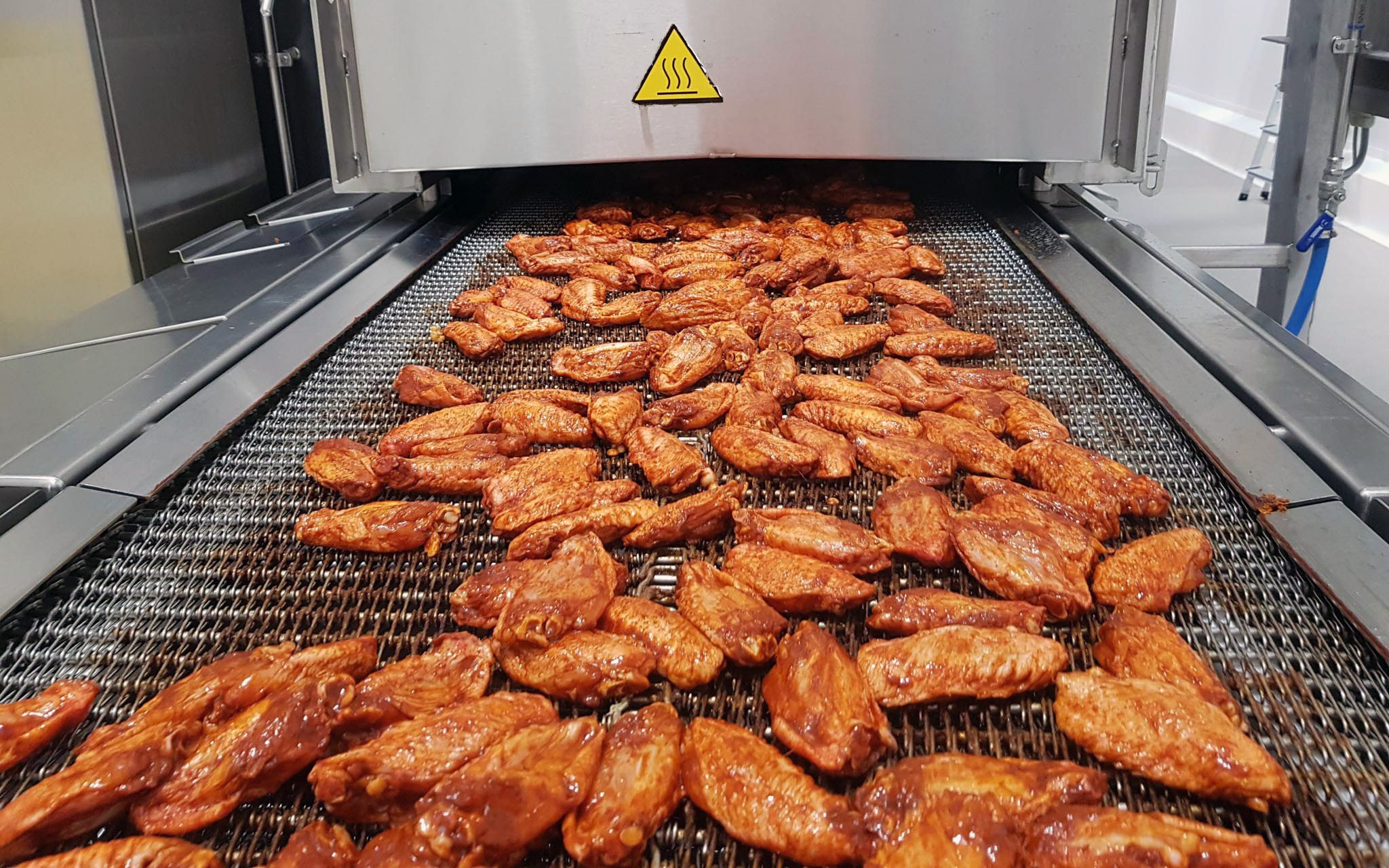
Eine sich entwickelnde Zusammenarbeit für beide Parteien
JBT stand in ständigem Dialog mit Norsk Kylling über den Standort der Geräte, die Installation des Anschlusses an das elektrische System und die Erfüllung anderer Anforderungen.
"Wir haben den Standort der Steuerschränke und den Anschluss angepasst, aber die Lösung für den Ofen selbst ist eher standardisiert", sagt Erland Leide. "Schon als wir den Ofen ursprünglich entwarfen, dachten wir an ein modulares System, so dass keine besonderen Anpassungen erforderlich waren. Die Zusammenarbeit mit Norsk Kylling hat uns dazu gebracht, den Ofen weiterzuentwickeln, da wir ihn auf der Grundlage der tatsächlichen Bedürfnisse und Anregungen des Unternehmens angepasst haben. Ihre detaillierte Anforderungsspezifikation und unser Dialog gaben uns wertvolle Informationen darüber, wie wir unsere Geräte besser entwickeln können, um die Anforderungen und Bedürfnisse unserer Kunden zu erfüllen."
Norsk Kylling hatte eine klare Vorstellung davon, wie die Lösungen funktionieren sollten. Sie wollten auch, dass jeder, der an dem Projekt beteiligt war, es verstand, sich engagierte und die Industrie weiter entwickelte. Für sie war JBT ein Lieferant, der über die Erfahrung und die Lebensmittelverarbeitungssysteme verfügte, die ihren Anforderungen entsprachen, und gleichzeitig flexibel und innovativ genug war, um einen Mehrwert für das Projekt zu liefern.
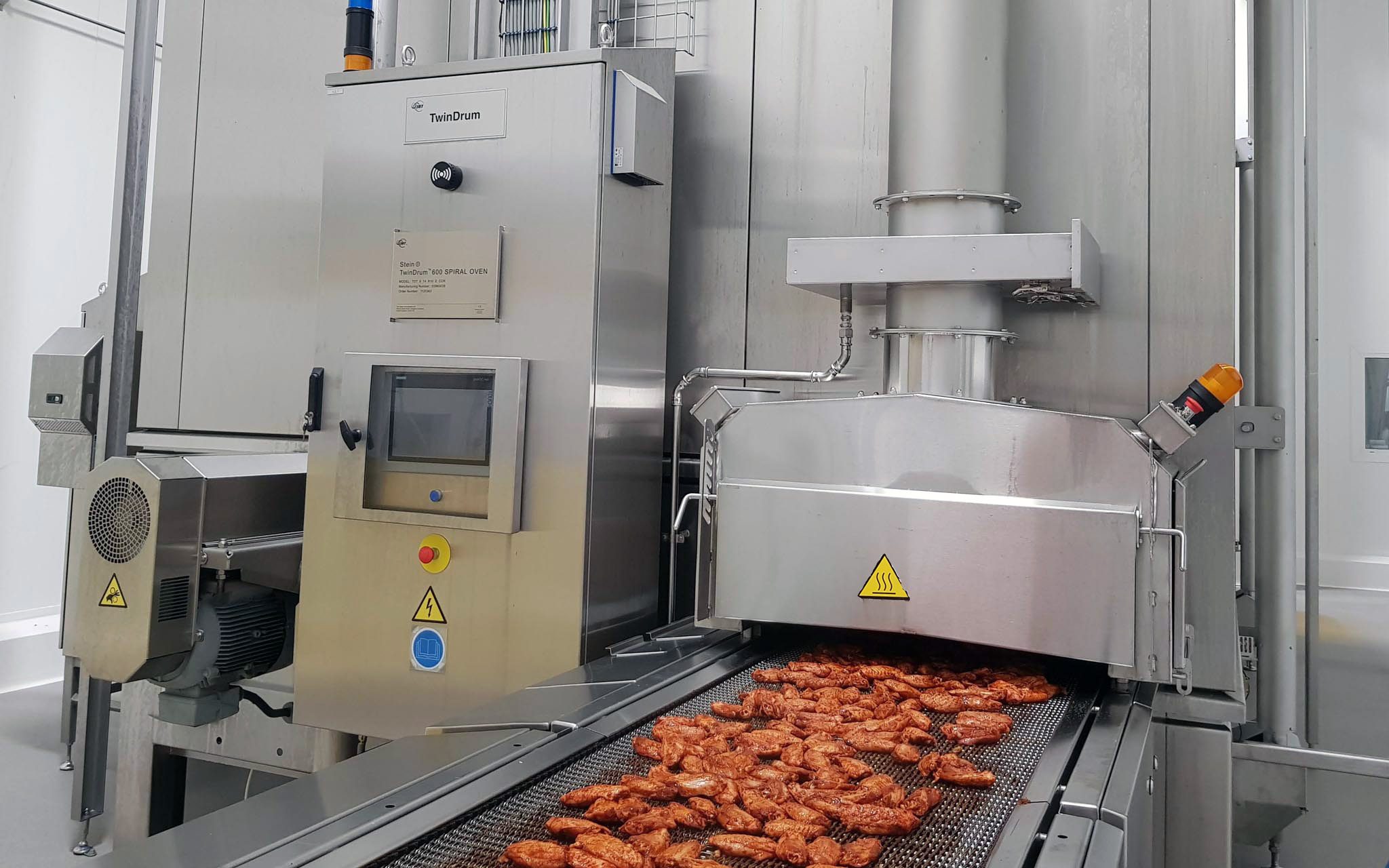
Eine Partnerschaft ohne Prestige
Um sicherzustellen, dass das Projekt so reibungslos wie möglich abläuft, hatte JBT ein spezielles Team zusammengestellt, das eng mit dem Team von Norsk Kylling zusammenarbeitete und so eine persönliche und zugleich professionelle Beziehung aufbaute.
"Während der gesamten Installations- und Inbetriebnahmephase waren wir fast ständig vor Ort, was zu einem echten Teamgeist und viel Engagement führte", sagt Teddy Svensson, Engineering Manager bei JBT. "Für uns steht der Kunde im Mittelpunkt. Wenn es Probleme gab und wir nicht vor Ort waren, sind wir sofort nach Orkanger gereist, um sie zu lösen."
Es ist wichtig, sich auf die Problemlösung zu konzentrieren, um eine gute Beziehung zu pflegen und ein erfolgreiches Projekt zu schaffen. "Wenn wir alle als Team ohne Prestige arbeiten, können wir optimale Lösungen finden und voneinander lernen", sagt Teddy Svensson.
JBT unterstützte Norsk Kylling auch bei der Entwicklung von Rezepten für höchste Erträge und schulte das Personal im Umgang mit den CIP-Systemen, um den Wasser-, Waschmittel- und Energieverbrauch zu optimieren.
"Die Zusammenarbeit mit JBT war perfekt, auch wenn wir beide manchmal das Gefühl hatten, dass es sich um ein anspruchsvolles Projekt handelt", sagt Håvard Staverlökk. "Man muss anerkennen, dass es Herausforderungen gibt und gemeinsam Lösungen finden. Ich würde sagen, dass sowohl JBT als auch Norsk Kylling abwechselnd unsere Herausforderungen bei diesem Projekt gelöst haben, und auf diese Weise haben wir es gemeinsam geschafft, das Projekt auf die bestmögliche Weise abzuschließen."